MY CODE CAN BE FOUND AT THE FOLLOWING LINK:
https://docs.google.com/document/d/1r1VQ7ZJ3Uyx4_Quf5kYepTnp9TEwRxh3qwmZ-R1DV8M/edit?usp=sharing
Hello, my name is Shaan, and I go to Mountain View High School. My main project is to create a hand gesture controlled robot, with a robotic arm. I used this website as a guide for my project. I have always been interested in raspberry pi, as they are inexpensive, and the projects you can create with them are abundant. I decided to do this project as it used Arduino, something that I have never seen, nor used before, and XBee. I thought that this project would be a great learning experience for me, and teach me more about software, electrical, and mechanical engineering. I really enjoyed the mechanical and electrical parts of my project, and found out that software was not for me. Although this project brought great frustration I was able to learn a lot. At Bluestamp you are put in a position where you are given help, but not the direct answer to the problem. You are forced to go out there and try new things, and do independent research, not only does this increase your researching skills, but it allows to problem solve without relaying on more experienced people. I really loved the way this camp was taught, most camps I have been to the instructors practically do the project for you, but here at Blustamp, I can truly call this project my own.
Shaan P – Final Milestone
Shaan P – Milestone #2
Shaan P – Milestone #1
My main difficulty with this project was setting up the circuit, since I do not have much experience with breadboards I had to do a lot of research to figure out how to set up the breadboard to do what I wanted it to do. Due to my lack of experience in breadboards I spent a couple of hours rewiring the entire circuit, to later find out I did not have a wire plugged in and the LED lights were not receiving any electricity. Below is a schematic that I used for my first milestone, using a breadboard was great for this project because I did not have to solder.
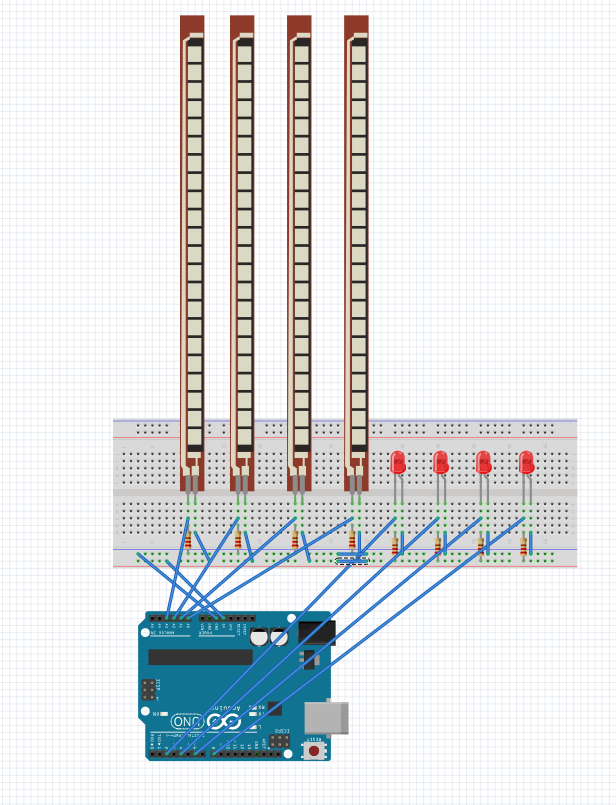
Comments
Wow! This is really cool!